Пружина подвески – это элемент подвески, который обеспечивает реакцию изменения клиренса на силовое воздействие дорожного покрытия при разных динамических нагрузках в результате передвижения по неровностям и боковых усилий при маневрах, кроме того она обеспечивает клиренс автомобиля в состоянии покоя. Отсюда, следует, что главные усилия компенсации переходят в упругость, именно поэтому пружину принято называть упругим элементом и величину сжатия в зависимости от действия сторонних сил высчитывают по закону Гука.
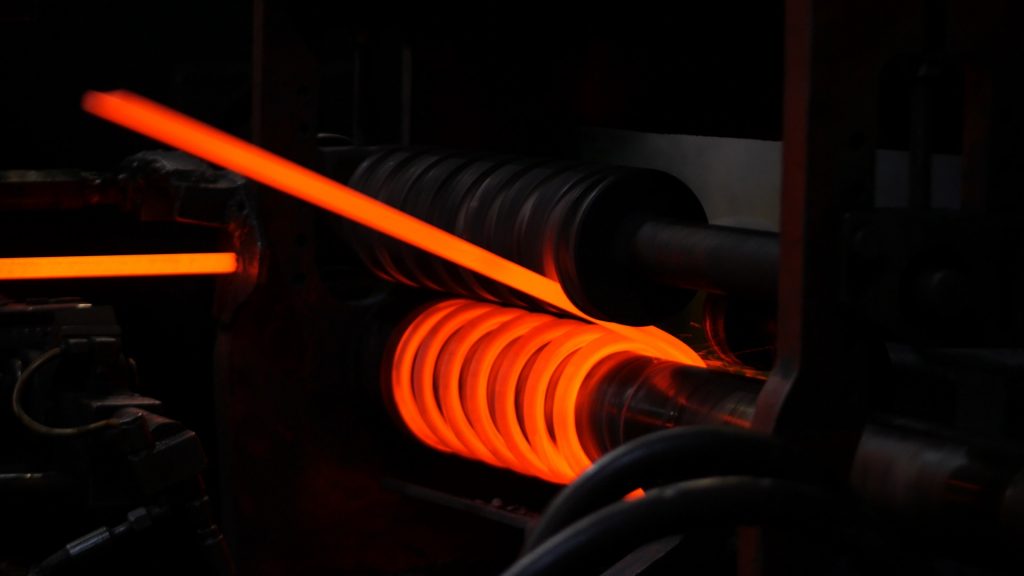
Журнал Auto3N решил посетить предприятие “КАС” (Ивановская обл.,г.Кинешма) и познакомить читателей с современными методами изготовления пружин.
Современные пружины имеют совершенно футуристическую форму, но принципы построения остаются незыблемыми. Современные пружины условно можно разделить на 4 основные формы: линейную, прогрессивную, с боковой нагрузкой (форма банана) и миниблок. Так же форму определяет навивка опорного витка. Разработка современных пружин подвески происходит с помощью математических моделей, а расчеты производятся в специализированных программах, что на выходе и дает сложные формы с определением допустимых нагрузок и долговечность. Компания КАС имеет собственные службы конструкторов и технологов для проектирования пружин подвески автомобиля любой сложности.
Изготовление пружин – это технологический процесс от получения и проверки сырья до испытания конечного изделия различными тестами, имитирующими эксплуатацию пружины в предельных режимах. Навивка пружин разными методами – это лишь малая часть в цепочке производства. За ним, как правило, следует комплекс термообработки, пластического упрочнения поверхности, нанесения лакокрасочного покрытия и упаковка.
На сегодняшний день есть два наиболее распространенных метода навивки пружин: первый – это метод горячей навивки, второй – метод холодной навивки. Оба метода производства пружин освоены на предприятии «КАС»
Методы изготовления пружин
Горячая навивка пружины – это метод производства пружин, который известен уже более века. За свое время производство пружин данным методом претерпело ряд изменений и сейчас это – достаточно проверенный и надежный метод получения пружины, но более дорогой по сравнению с методом холодной навивки. В формирование цены входят энерго затраты на разогрев заготовки, обработка и нарезка прутков как дополнительная операция, дорогостоящая оснастка – копир. К плюсам можно отнести стабильность формы и относительную простоту настройки, в качестве исходного материала можно использовать проволоку большего диаметра, а так же пружин переменного сечения. Как правило, применяется для получения пружин цилиндрической или конической формы, а так же с одним подвитым витком.
Холодная навивка более современный метод по сравнению с горячей навивкой, имеет как ряд ограничений, так и преимуществ. Ограничения, в первую очередь, касаются диаметра прутка проволоки, как правило, он ограничивается диаметром 16 мм. Это связанно с внутренними напряжениями, которые концентрируются в металле после навивки. С другой стороны – ряд преимуществ: относительно быстрая перенастройка оборудования для изготовления пружин разной формы особенно из одного диаметра бунта, быстрое внедрение в производство из-за простой оснастки. Основное преимущество- это форма получаемых пружин: они могут быть не только цилиндрическими и коническими, но и прогрессивные, с боковой нагрузкой и миниблоки.
На предприятии КАС используются оба метода производства пружин. Компания с прошлого века является традиционным поставщиком на конвейера российских автосборочных заводов и имеет все необходимые компетенции и опыт для изготовления пружин нужного качества.
Есть мнения, что тот или иной метод получения пружины в большей или меньшей мере влияет на долговечность и эксплуатацию пружин подвески, что на самом деле не совсем верно. Вопрос выбора метода изготовления пружин лежит в плоскости объема производства и рентабельности. Такие факторы, как скорость освоения номенклатуры, изготовления оснастки, объема производства и формы пружины являются главными критериями для выбора метода изготовления.
Дробеструйный или дробеметный наклеп – распространенный метод упрочнения пружин, увеличивающий их динамическую прочность. Обработке дробью пружины подвергаются после термических операций в том числе чтобы убрать внутренние напряжения. Сущность процесса заключается в ударном воздействии потока стальной или чугунной дроби диаметром 0,4-1,8 мм. Дробь разгоняется до определенной скорости с помощью вращающегося ротора с лопарками или струи эмульсии или воздуха. К основным параметрам интенсивности наклепа относятся глубина упрочнения и остаточные сжимающие напряжения. Так же дробенаклеп подготавливает поверхность для качественного нанесения покрытия.
На предприятии КАС все пружины проходят обязательную проверку и сортировку, трехкратное обжатие. Данные методы проверки гарантируют соответствие заданным параметрам и разделение пружин по группам нагрузки. Обжатие пружин до полного соприкосновения витков предотвращается «просадку» пружин после установки на транспортное средство. Данная операция проводиться на автомате с ЧПУ, где одновременно проверяется усилие пружин на заданной высоте и сортируется по группам нагрузки.
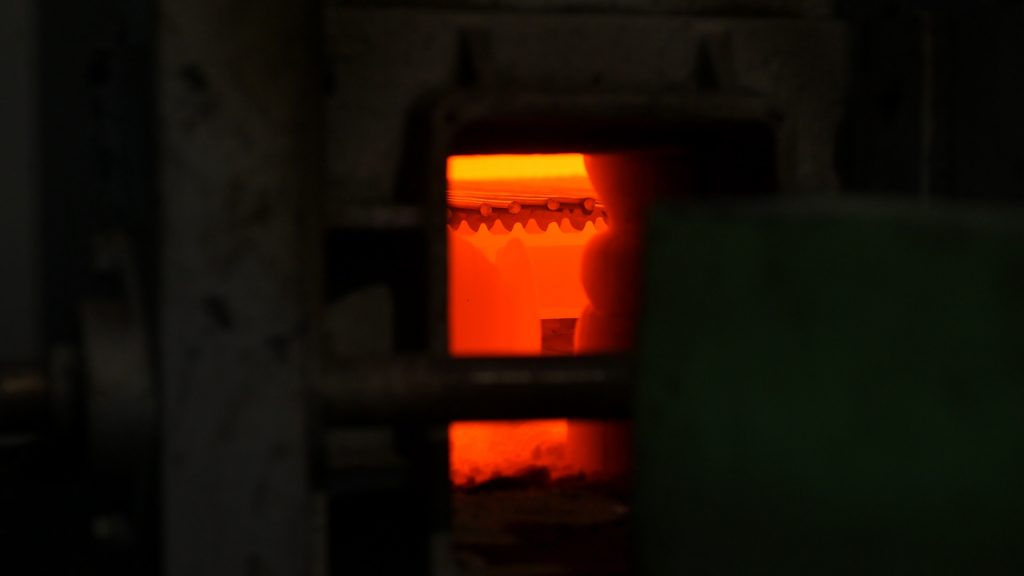
На практике выбор сырья, дробеметная обработка и правильно подобранные режимы термообработки влияют на характеристики пружины и ее циклическую долговечность.
Окраска пружин влияет на коррозионную стойкость пружин, предотвращая коррозию материала от внешних атмосферных факторов. Для окраски на предприятии КАС используется поточная линия окраски с предварительной обработкой поверхности цинк-фосфатным покрытием и последующей полимеризацией порошковой краски, что дает гарантированную стойкость пружины до 750 часов в камере соляного тумана имитирующего наиболее жесткие условия эксплуатации.
Многолетний опыт работы, необходимое оборудование для производства и испытания в купе с качественным материалом, позволяет изготавливать пружины, отвечающие современным требованиям, как по эксплуатационным показателям, так и экономическим. Миссия компании КАС – создавать качественные автокомпоненты, тем самым улучшая качество жизни и повышая глобальный уровень безопасности дорожного движения. Стремясь к этому, наше предприятие в десятке первых компаний получила сертификат качества IATF 16949. Так компания, по мимо пружин, производит штанги и стойки стабилизатора, поршни тормозной системы, гидроцилиндры, шаровые пальцы и много других продуктов. Такой подход позволил компании завоевать рынок основных конвейерных поставок на территории российской федерации и стать самым крупным поставщиком поршней тормозной системы на заводы ZF (TRW) в Европе.
редакция благодарит Павла Шаповалова, заместителя коммерческого директора по маркетингу за предоставленные материалы.